Novembre 2022
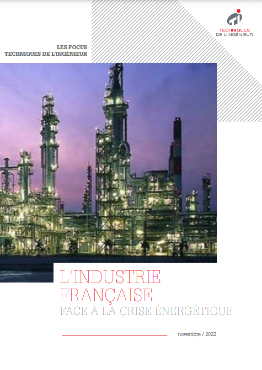
L'industrie française face à la crise énergétique
La crise énergétique touche durement l'industrie française.
RECHERCHEZ parmi plus de 10 000 articles de référence ou pratiques et 4 000 articles d'actualité
PAR DOMAINE D'EXPERTISE
PAR SECTEUR INDUSTRIEL
PAR MOTS-CLES
NAVIGUER DANS LA
CARTOGRAPHIE INTERACTIVE
DÉCOUVREZ toute l'actualité, la veille technologique GRATUITE, les études de cas et les événements de chaque secteur de l'industrie.
En vertu des objectifs de diminution des émissions de gaz à effet de serre, l’hydrogène est devenu un vecteur énergétique pertinent pour décarboner l’industrie, les transports, les réseaux de gaz et d’électricité. L’Union européenne, qui contribue largement au dynamisme économique de ce secteur, a établi une stratégie dans le cadre du Pacte vert (Green Deal) avec des objectifs pour 2030 et 2050, qui font appel aux énergies éolienne et solaire photovoltaïque. Des projets importants d’intérêt européen commun (PIIEC) sont lancés pour soutenir l’usage de l’hydrogène comme vecteur d’énergie. À l’échelle de la France, des objectifs stratégiques ambitieux, impliquant un investissement de 7 milliards d’euros pour 2030, sont consacrés à l’hydrogène.
Les systèmes thermiques à sorption solide représentent une gamme de composants majeurs pour l’utilisation rationnelle de l’énergie. Ils ont d’ores et déjà̀ trouvé plusieurs niches de développement : roues dessiccantes et groupes refroidisseurs de liquide à faible température de régénération pour l’adsorption, production de froid à température négative, stockage de froid pour le transport de denrées et stockage thermique pour la réaction chimique. De plus, de nouveaux produits sont très innovants : capture d’eau atmosphérique, valorisation, stockage et transport de chaleur fatale. Enfin, l’émergence des MOF ainsi que des mises en forme innovantes ouvre de nouvelles perspectives pour réduire le poids et le volume de ces systèmes et entendre ainsi leur marché.
La modélisation d’un système de pile à combustible à membrane échangeuse de protons (PEMFC) est essentielle pour améliorer ses performances, en permettant notamment l’accès à ses états internes. Il existe diverses méthodes de modélisation spatiale, chacune avec ses avantages et inconvénients. Il est crucial de les connaître afin de choisir le modèle le plus adapté à l’objectif visé. La validation d’un tel modèle nécessite l’utilisation de données expérimentales variées, ainsi que deux étapes cruciales : une calibration des paramètres indéterminés et une vérification des résultats. Pour illustrer ces concepts, un modèle 1D dynamique, biphasique et isotherme est présenté.
Sans fiabilité de l’outil de production, il n’y a pas de satisfaction du client, pas de compétitivité ni de performance. La maintenance, autrefois simple entretien du matériel, est ainsi devenue un processus support des activités de réalisation du produit, qui, comme tous les processus, doit être maîtrisé pour atteindre les objectifs de l’entreprise en termes de qualité, coûts et délai de fabrication.
La version 2015 de la norme ISO 9001 accorde une place plus importante à la gestion des risques associés à l’activité et donne ainsi une dimension stratégique au processus maintenance, garant de la disponibilité des équipements.
Mais comment mettre en place une maintenance efficace de l’outil de production ? Nul besoin de théorie révolutionnaire ni d’outils sophistiqués ! Il s’agit d’abord de bien définir la stratégie à appliquer, puis de mettre en œuvre le PDCA : planifier, mettre en œuvre, suivre l’efficacité du processus maintenance grâce à des indicateurs pertinents et l’améliorer en continu.
Amélioration des performances, Certification ISO 9001, Management intégré...
Vous devez guider les acteurs de la production dans la mise en œuvre ou l’amélioration de leurs processus. La production de produit ou de service est une phase majeure dans la création de valeur pour les clients, puisqu’il supporte les activités dont découlent directement les produits et services fournis aux clients. Ses éventuelles défaillances peuvent affecter la satisfaction client, si elles ne sont pas détectées à temps. Il convient donc de s’assurer que toutes les conditions de maîtrise sont identifiées et respectées.
Cette fiche vous donne quelques clés pour maîtriser les processus de production ou de prestations de service de votre organisme.
Amélioration des performances, Certification ISO 9001, Management intégré...
Des défaillances pouvant affecter le fonctionnement du moyen de production, il est nécessaire de mettre en place une méthode d’analyse de la fiabilité afin de les identifier. L’AMDEC est l’une de ces méthodes. À partir de cette analyse, vous serez en mesure d’estimer les risques liés aux défaillances, puis de mettre en place des actions correctives lors de l’exploitation ou de la maintenance du moyen.
Le présent document définit d’une part la méthode d’analyse des modes de défaillance, de leurs effets et de leur criticité, ou AMDEC, et son mode d’application pour les moyens de production et moyens indirectement liés à un système de production. Il vous explique, d’autre part, la méthode pour mettre en œuvre une analyse AMDEC moyen.
Amélioration des performances, Certification ISO 9001, Management intégré...
TECHNIQUES DE L'INGENIEUR
L'EXPERTISE TECHNIQUE ET SCIENTIFIQUE
DE RÉFÉRENCE
Avec Techniques de l'Ingénieur, retrouvez tous les articles scientifiques et techniques : base de données, veille technologique, documentation et expertise technique
Plus de 10 000 articles de référence, fiches pratiques et articles interactifs validés par les comités scientifiques
Toute l'actualité, la veille technologique, les études de cas et les événements de chaque secteur de l'industrie
Automatique - Robotique | Biomédical - Pharma | Construction et travaux publics | Électronique - Photonique | Énergies | Environnement - Sécurité | Génie industriel | Ingénierie des transports | Innovation | Matériaux | Mécanique | Mesures - Analyses | Procédés chimie - bio - agro | Sciences fondamentales | Technologies de l'information
ACCUEIL | A PROPOS | ANNUAIRE AUTEURS | EXPERTS SCIENTIFIQUES | PUBLICITÉ | PLAN DU SITE | MENTIONS LÉGALES | RGPD | COOKIES | AIDE & FAQ | CONTACT
PAIEMENT
SÉCURISÉ
OUVERTURE RAPIDE
DE VOS DROITS
ASSISTANCE TÉLÉPHONIQUE
+33 (0)1 53 35 20 20